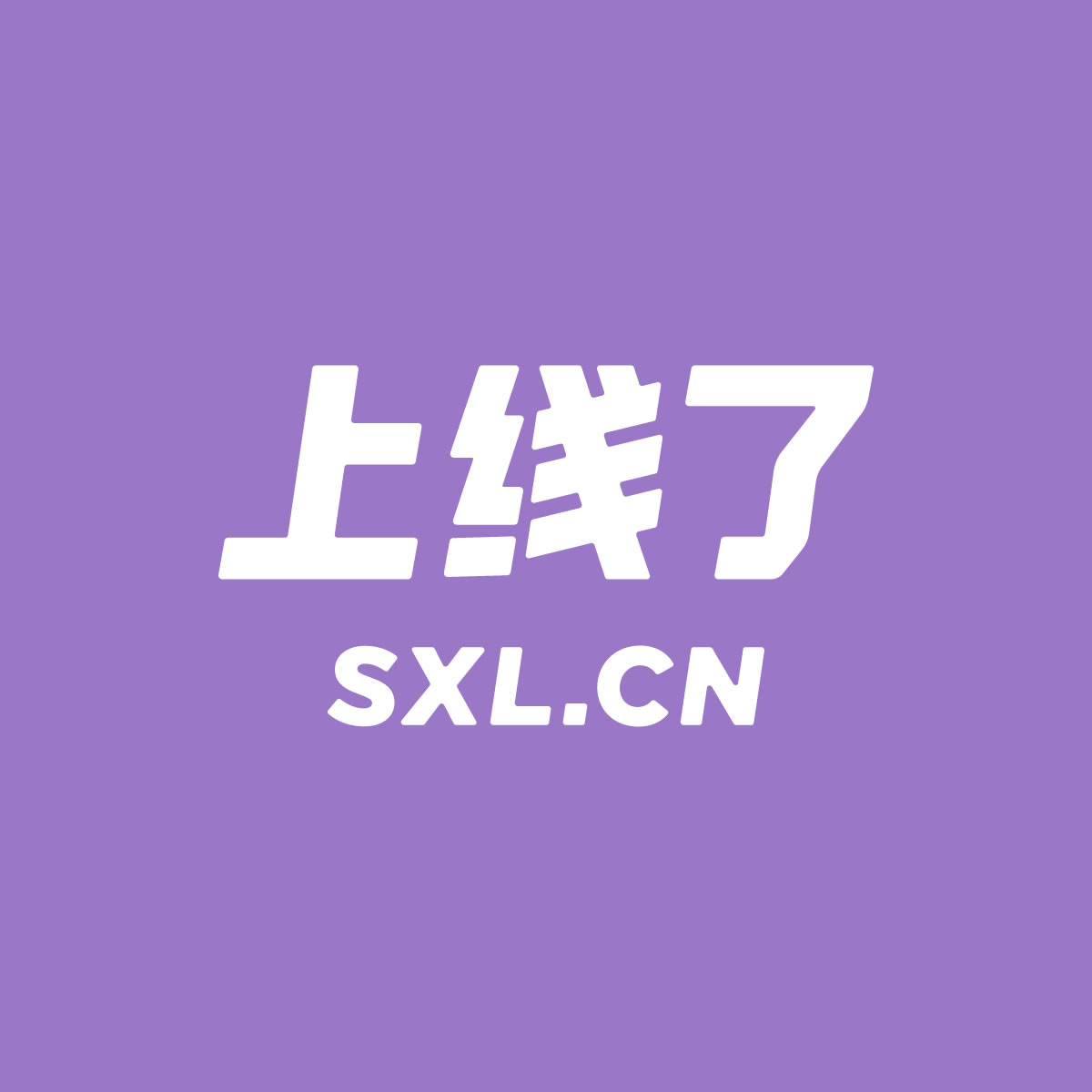
案例研究
I 激光加工视觉定位系统
3C组装视觉定位
精密金属制品激光加工
改造前,企业采用人工肉眼定位的方式加工材料,准确率极低且材料需要做大量留白,生产浪费极大。
改造后,定位精度可提高到25μm左右,加工材料无需大量留白,极大的提高了生产良率,节约了大量生产材料,增加了企业效益。激光打标视觉定位系统
医疗器械激光加工
改造前,企业采用人工手工摆放工件加传感器的方式定位,工人分白班、夜班每天每台加工50000片工件,当工件的位置出现偏差时且不能统一方向送料时,由于传感器无法感知,导致激光雕刻位置也出现偏,产品成为不合格品。
改造后,激光雕刻位置跟随工件保持一致,产量提高到每天每台75000片工件,极大提高了企业的生产良率和效率,并且显著降低了产线工人的劳动强度。激光精密加工视觉引导
3C类电子产品激光加工
改造前,企业采用自动化加传感器的方式定位被加工工件,当工件的位置出现偏差时,由于传感器无法感知,导致激光雕刻位置也出现偏,产品雕刻图案一致性较差。
改造后,通过视觉可以及时发现工件位置偏差,系统对偏差做出补偿,使得激光雕刻位置跟随工件保持一致,极大提高了企业的生产良率。飞行激光雕刻视觉系统
手机零件飞行激光雕刻视觉系统
改造前,企业采用人工手工摆放工件加传感器的方式定位,每小时加工2500片工件,当工件的位置出现偏差时且不能统一方向送料时,由于传感器无法感知,导致激光雕刻位置也出现偏,产品成为不合格品。
改造后,激光雕刻位置跟随工件保持一致,产量提高到每小时约4000片,极大提高了企业的生产良率和效率,并且显著降低了产线工人的劳动强度。I 半导体检测设备
表面微观检测产品
4英寸晶圆AOI检测设备
改造前,企业采用人工加电子显微镜的方式检测晶圆片,单片检测时间久(30分钟以上)且检测内容不全面。
改造后,检测产品表面5μm直径的异物或缺损检测,单片检测时间缩短到2分钟且可以生成全面的检测报告,极大的提高了企业生产效率。
霍夫纳格智能科技(嘉兴)有限公司
Copyright (C) 2023 HOFFNUNG CORPORATION. All Rights Reserved.